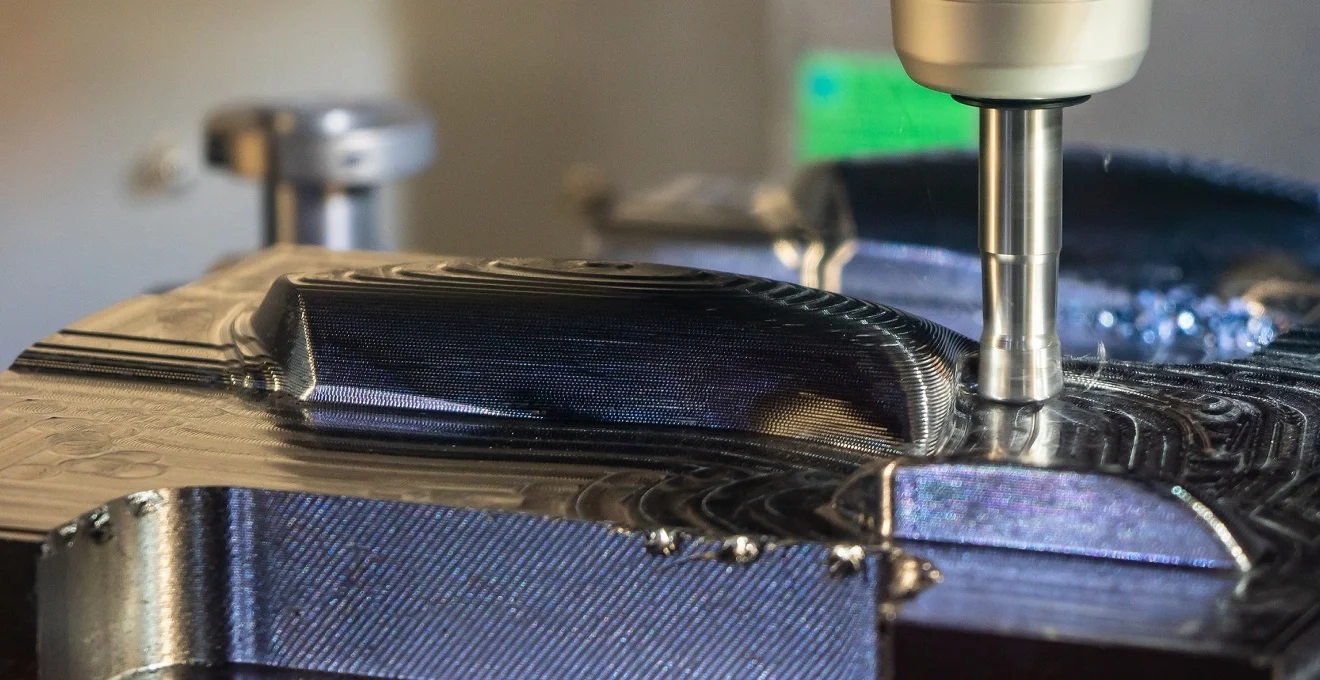
Friction stir welding (FSW) has revolutionized the joining of materials, particularly in industries demanding high-strength, defect-free welds. This solid-state welding process excels in joining difficult-to-weld alloys and dissimilar materials, offering significant advantages over traditional fusion welding techniques. As industries continue to push the boundaries of material science and engineering, optimizing FSW becomes crucial for achieving superior joint quality, improved efficiency, and expanded application possibilities.
Fundamentals of Friction Stir Welding Technology
Friction stir welding technology relies on a non-consumable rotating tool to generate frictional heat and mechanically mix materials at the joint interface. This process creates a plasticized region of material that, upon cooling, forms a high-strength, solid-state bond. Unlike conventional welding methods, FSW occurs below the melting point of the materials being joined, resulting in welds with minimal defects and superior mechanical properties.
The FSW process involves plunging a specially designed tool into the workpiece material. The tool consists of two main components: a shoulder that generates frictional heat and prevents material expulsion, and a pin that stirs and mixes the plasticized material. As the tool rotates and traverses along the joint line, it creates three distinct zones: the stir zone (SZ), the thermomechanically affected zone (TMAZ), and the heat-affected zone (HAZ).
Understanding the microstructural changes and material flow behavior in these zones is essential for optimizing the FSW process. The SZ typically exhibits fine, equiaxed grains due to dynamic recrystallization, while the TMAZ shows elongated grains oriented in the direction of material flow. The HAZ experiences thermal cycling without significant plastic deformation, potentially leading to grain growth or precipitation changes in some alloys.
Material Selection and Preparation for FSW
Successful implementation of FSW begins with careful material selection and preparation. While FSW is particularly effective for aluminum alloys, it can also be applied to other materials such as steels, titanium alloys, and even polymers. Each material presents unique challenges and requires specific considerations for optimal welding performance.
Aluminum Alloy Considerations in FSW
Aluminum alloys remain the most common materials joined using FSW due to their excellent weldability and widespread use in aerospace and automotive industries. When selecting aluminum alloys for FSW, consider the following factors:
- Alloy composition and temper condition
- Thermal conductivity and specific heat capacity
- Strength and ductility requirements
- Potential for post-weld heat treatment
- Corrosion resistance in the intended application
For example, 2xxx and 7xxx series aluminum alloys, known for their high strength but poor fusion weldability, are excellent candidates for FSW. These alloys often experience significant strength reduction in the HAZ, necessitating careful process parameter selection to minimize this effect.
Steel and Titanium FSW Challenges
Welding steels and titanium alloys using FSW presents additional challenges due to their higher melting points and lower thermal conductivity compared to aluminum. These materials require specialized tool materials and designs to withstand the extreme temperatures and forces involved in the process.
For steel FSW, tool wear becomes a critical factor, with PCBN (Polycrystalline Cubic Boron Nitride) and tungsten-based alloys being common choices for tool materials. Titanium FSW often employs tungsten-rhenium alloys or advanced ceramics to combat rapid tool wear and maintain weld quality throughout the process.
Surface Preparation Techniques for Enhanced Weld Quality
Proper surface preparation is crucial for achieving high-quality FSW joints. Key considerations include:
- Removal of surface oxides and contaminants
- Ensuring consistent material thickness across the weld line
- Maintaining proper joint fit-up and alignment
- Consideration of surface roughness effects on material flow
For aluminum alloys, a simple degreasing and wire brushing process may suffice. However, for reactive materials like titanium, more stringent cleaning procedures and inert gas shielding may be necessary to prevent oxidation during welding.
Tool Material Selection for Specific Workpiece Materials
Selecting the appropriate tool material is critical for FSW success, particularly when welding high-temperature materials or abrasive alloys. Common tool materials include:
- Tool steels (e.g., H13) for aluminum alloys
- Tungsten carbide for more abrasive aluminum alloys
- PCBN for steels and titanium alloys
- Tungsten-rhenium alloys for extreme high-temperature applications
The ideal tool material should possess high hot hardness, good thermal stability, and resistance to wear and oxidation under FSW conditions. Additionally, the tool geometry must be optimized for the specific material being welded to ensure efficient material flow and heat generation.
FSW Process Parameter Optimization
Optimizing FSW process parameters is crucial for achieving high-quality welds consistently. The primary parameters that influence weld quality include rotational speed, traverse speed, axial force, and tool geometry. These parameters must be carefully balanced to generate sufficient frictional heat and material flow without introducing defects or compromising joint properties.
Rotational and Traverse Speed Calibration
The ratio of rotational speed to traverse speed, often referred to as the weld pitch, significantly affects the heat input and material flow in FSW. Higher rotational speeds generally increase heat generation and material mixing, while faster traverse speeds can lead to insufficient heating and poor consolidation.
For aluminum alloys, typical rotational speeds range from 400 to 1500 RPM, with traverse speeds varying from 100 to 1000 mm/min. However, these values can differ significantly for other materials. For instance, steel FSW may require rotational speeds as low as 200 RPM due to the higher strength and lower thermal conductivity of the material.
Axial Force and Plunge Depth Control
The axial force applied during FSW directly influences the frictional heat generation and material consolidation. Insufficient axial force can lead to lack of penetration and void formation, while excessive force may cause flash and tool wear. Modern FSW machines often employ force-controlled systems to maintain consistent axial force throughout the weld.
Plunge depth, closely related to axial force, determines the extent of tool shoulder contact with the workpiece surface. Proper plunge depth ensures adequate heat generation and material containment. For most applications, a slight tilting of the tool (typically 2-4 degrees) helps improve material flow and weld surface quality.
Tool Tilt Angle and Shoulder Diameter Effects
The tool tilt angle and shoulder diameter play crucial roles in material flow and heat generation during FSW. A slight tilt angle (typically 2-4 degrees) helps improve material flow from the leading edge to the trailing edge of the tool, enhancing weld quality and surface finish.
The shoulder diameter affects the size of the heat-affected zone and the overall heat input into the weld. Larger shoulder diameters generally provide more stable welding conditions but may also increase the HAZ size. Optimizing the shoulder diameter for specific material thicknesses and joint configurations is essential for achieving the desired weld properties.
Temperature Monitoring and Heat Input Regulation
Monitoring and controlling the temperature during FSW is crucial for maintaining consistent weld quality and preventing defects. Various methods can be employed for temperature measurement, including:
- Embedded thermocouples in the workpiece or backing plate
- Infrared thermal imaging cameras
- Tool-integrated temperature sensors
Advanced FSW systems may incorporate closed-loop temperature control, adjusting process parameters in real-time to maintain optimal welding conditions. This becomes particularly important when welding materials with narrow processing windows or when joining dissimilar materials with different thermal properties.
Advanced FSW Techniques for Complex Geometries
As FSW technology matures, new techniques are being developed to address complex geometries and challenging applications. These advanced methods expand the capabilities of FSW beyond simple butt and lap joints, enabling the welding of curved surfaces, variable thickness materials, and multi-directional joints.
One such technique is bobbin tool FSW, which uses a double-sided tool to weld materials from both sides simultaneously. This method is particularly useful for welding hollow structures or materials that are difficult to back up, such as aircraft fuselage panels.
Another innovative approach is stationary shoulder FSW, where only the pin rotates while the shoulder remains stationary. This technique reduces heat input and minimizes the HAZ, making it ideal for welding heat-sensitive materials or thin sheets.
Adaptive control systems are also being implemented in FSW to automatically adjust process parameters based on real-time feedback. These systems can compensate for variations in material properties, joint geometry, or environmental conditions, ensuring consistent weld quality across complex parts.
Quality Assurance and Defect Mitigation in FSW
Ensuring consistent weld quality and minimizing defects are paramount in FSW applications. A comprehensive quality assurance program should include both in-process monitoring and post-weld inspection techniques to detect and prevent potential issues.
Non-Destructive Testing Methods for FSW Joints
Several non-destructive testing (NDT) methods can be employed to evaluate FSW joint quality:
- Ultrasonic testing for internal defect detection
- Radiographic inspection for volumetric defect analysis
- Eddy current testing for surface and near-surface defects
- Phased array ultrasonic testing for high-resolution imaging of weld zones
Each NDT method has its strengths and limitations, and the choice of technique often depends on the specific material, joint configuration, and critical defect types for the application.
Common FSW Defects: Identification and Prevention
Understanding common FSW defects and their root causes is essential for developing effective prevention strategies. Some typical FSW defects include:
- Tunnel defects or wormholes due to insufficient material consolidation
- Lack of penetration resulting from inadequate pin length or plunge depth
- Surface galling caused by excessive heat input or improper tool design
- Kissing bond defects from insufficient breaking up of oxide layers
Preventing these defects often involves careful optimization of process parameters, tool design, and material preparation techniques. In-process monitoring systems, such as force sensors and thermal cameras, can provide early detection of conditions that may lead to defect formation.
Microstructural Analysis of FSW Weld Zones
Microstructural analysis plays a crucial role in understanding the quality and performance of FSW joints. The distinct zones created during FSW (SZ, TMAZ, and HAZ) each exhibit unique microstructural features that influence the overall joint properties.
Techniques such as optical microscopy, scanning electron microscopy (SEM), and electron backscatter diffraction (EBSD) are commonly used to characterize FSW microstructures. These analyses can reveal important information about grain size, texture, precipitate distribution, and potential defects at the microstructural level.
Mechanical Property Evaluation of FSW Joints
Comprehensive mechanical testing is essential to validate the performance of FSW joints. Common tests include:
- Tensile testing for strength and ductility assessment
- Bend testing to evaluate joint ductility and surface quality
- Fatigue testing for cyclic loading performance
- Hardness mapping to characterize property variations across the weld zones
- Fracture toughness testing for critical structural applications
These tests provide valuable data for optimizing FSW parameters and validating joint performance for specific applications. It's important to consider both static and dynamic loading conditions, as well as environmental factors that may affect long-term joint integrity.
Industrial Applications and Future Trends in FSW Technology
FSW has found widespread adoption in various industries, with continuous expansion into new applications. The aerospace sector remains a primary user of FSW technology, particularly for joining large aluminum structures such as rocket fuel tanks and aircraft fuselages. The automotive industry is increasingly adopting FSW for lightweight vehicle construction, joining aluminum body panels and frame components.
Emerging trends in FSW technology include:
- Integration with robotic systems for increased flexibility and automation
- Development of hybrid welding processes combining FSW with other joining techniques
- Expansion into new material combinations, including metal-polymer joints
- Implementation of machine learning algorithms for process optimization and defect prediction
- Miniaturization of FSW tools for micro-joining applications
As industries continue to demand lighter, stronger, and more efficient structures, FSW is poised to play an increasingly important role in advanced manufacturing processes. The ongoing development of new tool materials, process variants, and control systems will further expand the capabilities and applications of this versatile joining technology.
By mastering the fundamentals of FSW and staying abreast of the latest advancements, engineers and manufacturers can harness the full potential of this innovative welding process to create high-performance, cost-effective solutions across a wide range of industries.